Total Cost of Ownership
In today’s food processing industry, businesses face rising energy costs, labor shortages, and stricter regulations—all while trying to maintain razor-thin profit margins. Investing in the right equipment can make or break operational success, but too many buyers focus solely on the sticker price. Enter Total Cost of Ownership (TCO): a smarter way to evaluate equipment by considering its full financial impact over time. TCO goes beyond the initial purchase to include operating costs, maintenance, downtime, and even disposal. For food processors, understanding TCO isn’t just a budgeting exercise—it’s a strategic advantage. Companies like Velec Systems are leading the charge by offering high-efficiency solutions designed to minimize TCO, helping businesses stay competitive in a challenging market.
Quick Takeaways
- TCO covers purchase price, energy, labor, maintenance, downtime, and disposal.
- Energy-efficient equipment slashes lifetime costs.
- Reliable machinery and preventive maintenance minimize downtime.
- Strong warranties (like Velec’s) cut long-term expenses.
What is TCO?
Total Cost of Ownership (TCO) is the complete cost of acquiring and operating a piece of food processing equipment throughout its lifecycle. It’s not just the upfront price tag—it’s the sum of energy bills, repair expenses, labor requirements, lost production from downtime, and the eventual cost of replacing or disposing of the machine. Think of TCO as the true price you pay, revealed only after years of use. For food processors, where efficiency and reliability are paramount, TCO offers a clearer picture than purchase price alone.
Why TCO Matters More Than Purchase Price
Focusing only on upfront costs is a common pitfall. Studies from SF Engineering suggest that the initial purchase price of food processing machinery often accounts for just 20-30% of its total cost over a decade. The rest? Hidden expenses like energy consumption, frequent repairs, and production halts. Imagine a small meat processor opting for a $10,000 slicer over a $15,000 model. Two years later, the cheaper machine’s breakdowns and inefficiency rack up $50,000 in losses—far exceeding the $5,000 saved upfront. In contrast, investing in durable, energy-efficient equipment can slash lifetime costs significantly. Here’s a quick comparison:
Equipment | Upfront Cost | 10-Year TCO | Key Difference |
---|---|---|---|
Machine A (Cheap) | $10,000 | $60,000 | High energy, frequent fixes |
Machine B (Premium) | $15,000 | $35,000 | Efficient, reliable |
TCO reveals the long game—and it’s one worth playing.
Key Factors Influencing TCO in Food Processing Equipment
Understanding what drives TCO helps buyers make informed choices. Here are the five biggest factors:
- Initial Purchase Price vs. Long-Term Costs
A budget-friendly conveyor might save $10,000 today, but if it fails after three years while a $15,000 model lasts ten, the TCO math flips fast. Premium equipment, like Velec Systems’ durable centrifugal machines, often pays off with fewer headaches and lower lifetime costs.
- Energy Efficiency and Utility Costs
Energy-intensive equipment can devour profits. A high-efficiency thermoformer, for instance, might use 500 kWh less per month, saving $100 at $0.20/kWh—$1,200 annually. BW Packaging notes upgrades can cut energy costs by up to 30%. Look for certifications like ENERGY STAR or Velec’s smart energy-saving features to keep utilities in check. - Maintenance and Repair Expenses
Unplanned repairs can cost 3-5 times more than preventive maintenance, per industry estimates. Equipment with modular designs, local spare parts, and strong warranties—like those from Velec Systems—reduces these expenses. A stainless steel system resistant to corrosion can also dodge costly replacements in wet environments. - Downtime and Productivity Losses
A single hour of downtime in a mid-sized plant can cost $5,000-$10,000 in lost output. Robust construction and automated monitoring (think Velec’s real-time diagnostics) minimize these risks, keeping production humming. - Labor Costs and Training Requirements
With labor costs climbing 5% annually, automation is a lifeline. Equipment with intuitive interfaces—like Velec’s sausage packaging systems—can cut training time by 20% and reduce human error, saving thousands in wages over time.
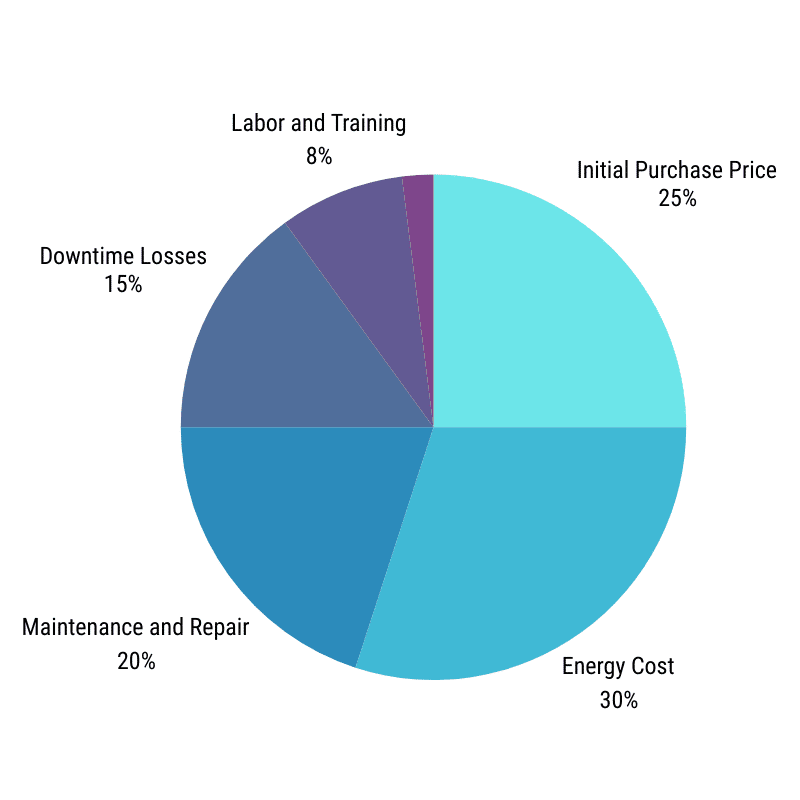
Strategies to Minimize TCO in Food Processing Equipment
Lowering TCO starts with smart decisions. Here’s how:
- Selecting the Right Equipment for Your Needs
Match equipment to production volume, scalability, and existing systems. A bakery scaling from 1,000 to 10,000 loaves daily needs a machine that grows with it—not one that maxes out early. Check energy ratings and warranty terms too. - Investing in Durable and Low-Maintenance Equipment
Stainless steel and self-cleaning systems (hallmarks of Velec’s designs) resist wear and tear. A 20% higher upfront cost might yield 50% lower TCO over a decade, thanks to fewer repairs and longer life. - Optimizing Energy and Water Consumption
Smart tech, like IoT sensors or automated shutoffs, trims utility bills. Velec Systems integrates these features to boost sustainability and savings. - Implementing Preventive Maintenance Programs
A simple schedule—weekly checks, quarterly deep cleans—can cut breakdowns by 25%, per industry data. It’s cheaper to replace a $50 part proactively than a $500 component after a failure.
How to Calculate TCO for Food Processing Equipment
Ready to crunch the numbers? Use this formula:
TCO = Initial Cost + (Ongoing Costs x Expected Asset Life)
Here’s the process:
- List Initial Costs: Equipment price, shipping, installation (e.g., $50,000 total).
- Estimate Annual Operating Costs: Energy ($5,000), labor ($3,000), supplies ($2,000) = $10,000/year.
- Factor in Maintenance and Downtime: $2,000/year for repairs, $1,000 for lost production.
- Project Lifespan and Disposal: 8 years, $1,000 to decommission.
Example: $50,000 + ($13,000 x 8) + $1,000 = $155,000 TCO.
Compare that to a $60,000 machine with $8,000 annual costs over 10 years ($140,000 TCO), and the “pricier” option wins. Velec Systems can help with tailored TCO assessments—contact them for a free consultation.
Case Studies: Real-World TCO Optimization
- Reducing TCO Through Energy-Efficient Equipment
A meat processor swapped outdated thermoformers for an automated, high-efficiency model. Result? Energy costs dropped 25%—$50,000 saved in year one—proving TCO beats short-term savings (Commercial Food Sanitation). - The Cost of Neglect: Poor TCO Planning
A bakery chain bought low-cost ovens to save $5,000 per unit. Within five years, frequent breakdowns and 30% higher energy use spiked operating costs by 40%. A $25,000 investment in reliable ovens could’ve saved $100,000 long-term. - Velec Systems in Action
A poultry processor adopted Velec’s centrifugal packaging system. Labor costs fell 15% due to automation, and energy use dropped 20% with smart controls. Over three years, TCO was 30% lower than competitors’ systems.
Common TCO Mistakes to Avoid
Even savvy buyers slip up. Watch out for:
- Short-Term Thinking: Picking price over quality doubles costs later.
- Ignoring Hidden Costs: Installation, training, and disposal add up. One processor overlooked water usage, doubling bills over five years.
- Skipping Research: Unreliable manufacturers or scarce parts inflate expenses. Velec’s robust support avoids this trap.
Conclusion: Making Smarter Equipment Investments
Understanding TCO in food processing equipment isn’t just about saving money—it’s about boosting profitability, sustainability, and competitiveness. Prioritizing energy efficiency, durability, and proactive maintenance turns equipment into a long-term asset, not a liability. Ready to lower your TCO and maximize efficiency? Velec Systems offers tailored, high-efficiency solutions to fit your needs. Contact them today for a free assessment and start optimizing your operation.
References
- SF Engineering. “Calculating the Total Cost of Ownership of Food Processing Machinery.”
- BW Packaging. “How to Calculate the TCO of Packaging Machinery.”
- Commercial Food Sanitation. “Calculating True Total Cost of Ownership.”
- Velec Systems. “Optimizing Sausage Packaging: Centrifugal Machines & TCO.”