Introduction
Sausage packaging has come a long way from the simple butcher paper and string. Today, innovative technologies and designs ensure sausages stay fresh, safe, and appealing to consumers. In this Ultimate Guide to Sausage Packaging, we’ll explore the fascinating journey of sausage packaging, from production to the latest trends, giving you an in-depth understanding of this crucial aspect of the meat industry.
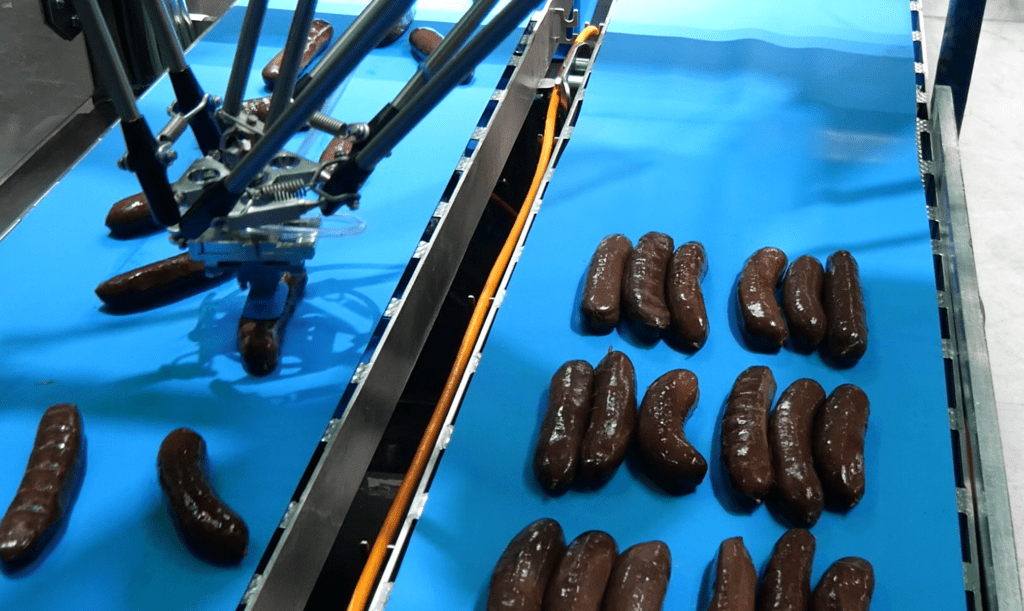
The Journey of a Sausage: From Production to Packaging
The journey of a sausage starts in the production facility, where high-quality ingredients are mixed and shaped. Once sausages are made, they enter the crucial stage of packaging. This stage is essential for maintaining the product’s integrity, extending shelf life, and making it attractive to consumers. Modern meat packaging equipment plays a vital role in this process, ensuring efficiency and consistency.
Imagine a bustling sausage factory where freshly made sausages move along conveyor belts. At each station, different machines handle various tasks. A vertical loader places sausages into appropriate packaging formats, ready for sealing while a stacks packaged sausages onto pallets for easy transportation, while a vertical loader places sausages into appropriate packaging formats, ready for sealing. Finally, a palletizer stacks packaged sausages onto pallets for easy transportation.
Understanding the Basics: Types of Sausage Packaging
Sausage packaging comes in various forms, each serving a specific purpose. The most common types include vacuum packaging, modified atmosphere packaging (MAP), and flow wrap packaging.
Vacuum Packaging: This method involves removing air from the package before sealing it. Vacuum packaging significantly extends the shelf life by reducing the oxygen levels that spoilage organisms need to thrive.
Modified Atmosphere Packaging (MAP): MAP replaces the air inside the package with a specific gas mixture, often carbon dioxide and nitrogen. This method also extends shelf life and helps maintain the sausage’s color and texture.
Flow Wrap Packaging: This versatile method wraps sausages in a continuous film, which is then sealed and cut to create individual packages. Flow wrap machines are highly efficient and ideal for high-speed production lines.
Thermoforming: This method involves heating a plastic sheet and forming it to mold tightly around the product. The shaped plastic is then cooled down and trimmed to create a sealed package.
Each packaging type has its benefits and is chosen based on the product’s requirements and market needs. For example, gourmet sausages might use MAP to maintain their premium quality, while mass-produced sausages might use flow wrap for efficiency.
Extending Shelf Life: Innovations in Sausage Packaging Technology
Innovations in packaging technology have revolutionized the sausage industry. Advanced thermoformer machines, for instance, mold plastic films into custom shapes, providing a tight and secure seal around each sausage. This not only extends the shelf life but also enhances the product’s presentation.
A study by Yerlikaya and Gokoglu (2010) found that sausages packaged using MAP had a shelf life of up to 28 days, compared to just 7 days for those packaged in regular air. Multiple other studies support this finding. Such advancements reduce food waste and improve profitability for manufacturers.
Moreover, these technologies ensure that sausages reach consumers in perfect condition, retaining their flavor, texture, and safety. By leveraging modern food packaging techniques, manufacturers can meet the high standards expected by today’s discerning consumers.
Custom Sausage Packaging: Tailoring to Market Needs
Custom packaging solutions are essential for meeting diverse market needs. Different types of sausages require specific packaging solutions to maintain their quality and appeal. For instance, fresh sausages need packaging that allows for some gas exchange, while dried or cured sausages require airtight packaging to prevent moisture ingress.
Using a vertical loader, sausages can be efficiently packed into various formats, such as trays, vacuum packs, and flow wraps. Custom packaging not only maintains the product’s quality but also enhances its visual appeal, crucial for attracting customers. For example, single-serve packaging is perfect for on-the-go consumers, while family-sized packs cater to larger households.
A packaging designer might work closely with a brand to create packaging that reflects its identity and meets consumer expectations. This collaboration ensures that the packaging is not only functional but also appealing and relevant in the marketplace.
Sustainable Sausage Packaging: Reducing Waste and Environmental Impact
Reducing packaging waste is a significant concern in today’s environmentally conscious world. Sustainable packaging practices help conserve resources and appeal to eco-conscious consumers. Innovations in sustainable packaging materials, such as biodegradable films and recyclable plastics, are helping reduce the environmental impact of sausage packaging.
Optimizing the packaging process using an automated packaging line can minimize material wastage and improve efficiency. For instance, lightweight materials reduce transportation costs and the overall carbon footprint. Additionally, designing packaging that can be easily recycled or reused further contributes to sustainability efforts.
The Importance of Hygienic Packaging and Processes
Hygienic packaging and processes are essential for maintaining the safety, quality, and shelf life of sausages. Preventing contamination is crucial, as it can occur at any stage of production and lead to foodborne illnesses or costly product recalls. Modern meat packaging equipment, such as vertical loaders and automated packaging lines, minimizes human contact with the product, thereby reducing contamination risks. Additionally, these machines are designed with materials and features that are easy to clean and sanitize, ensuring a high level of hygiene throughout the packaging process.
Maintaining hygienic standards also helps meet stringent food safety regulations set by bodies like the FDA and EFSA. Compliance with these regulations not only ensures consumer safety but also builds trust and opens up international market opportunities. Advanced packaging technologies, such as antimicrobial films and automated systems, further enhance product safety by inhibiting bacterial growth and maintaining a clean packaging environment. By prioritizing hygiene, sausage manufacturers can protect consumers, uphold their brand reputation, and ensure long-term success in a competitive market.
Design Matters: The Art and Science of Sausage Packaging Design
Packaging design is a critical aspect of sausage packaging that affects both functionality and aesthetics. A well-designed package protects the sausage, provides information to consumers, and stands out on the shelves. Key elements of effective packaging design include clear labeling, attractive graphics, and convenient features like resealable closures.
Thermoformers are widely used in the meat industry to create custom-shaped packages that fit sausages perfectly. This type of packaging not only looks appealing but also offers superior protection against external elements. For example, thermoformed packages can be designed with compartments to hold condiments or dipping sauces, adding value for the consumer.
Packaging design also plays a crucial role in brand differentiation. Unique shapes, colors, and materials can help a product stand out in a crowded marketplace. Additionally, transparent packaging can allow consumers to see the product inside, building trust and encouraging purchase.
Behind the Scenes: The Role of Automation and Machinery
Automation plays a vital role in modern sausage packaging. Automated packaging lines incorporate various machines, including palletizers, vertical loaders, thermoformers, and flow wrap systems, to streamline the packaging process. These automated systems increase production speed, reduce labor costs, and improve overall efficiency.
Automated packaging lines also ensure consistent quality by minimizing human error. For instance, automated thermoforming machines can precisely control the amount of packaging material used, reducing waste and ensuring a tight seal around the sausages. Additionally, automation allows for better tracking and monitoring of the packaging process, ensuring that any issues are quickly identified and addressed.
The integration of robotics in packaging lines has further enhanced automation capabilities. Robots can handle tasks like loading sausages into packaging machines, stacking finished products, and performing quality checks. This not only speeds up the process but also reduces the risk of contamination by minimizing human contact with the product.
Future Trends: What’s Next in Sausage Packaging?
Smart Packaging:
The sausage packaging industry is continuously evolving, with new innovations emerging to address various challenges. One notable trend is the development of smart packaging technologies, which use sensors and indicators to monitor the condition of the packaged product. These technologies can provide real-time information about the sausage’s freshness, ensuring that consumers receive the best quality product. For instance, smart packaging can include temperature-sensitive labels that change color if the sausages have been exposed to temperatures outside the safe range, alerting both retailers and consumers to potential spoilage.
Smart packaging also offers enhanced traceability. By incorporating QR codes or RFID tags, consumers can access detailed information about the product’s origin, production date, and even the journey it took to reach the store. This transparency not only builds consumer trust but also allows manufacturers to quickly identify and address any issues in the supply chain.
Antimicrobial Films
Another innovation is the use of advanced materials, such as antimicrobial films, which help extend the shelf life of sausages by inhibiting bacterial growth. These films are embedded with natural or synthetic antimicrobial agents that prevent the growth of harmful bacteria, keeping the sausages safe and fresh for longer periods. For example, packaging films infused with silver nanoparticles or essential oils like oregano and thyme can provide continuous antimicrobial protection, reducing the risk of contamination and spoilage.
In addition to antimicrobial properties, researchers are exploring packaging materials that can actively interact with the food product to maintain its quality. For example, oxygen scavengers and ethylene absorbers can be incorporated into packaging to remove unwanted gases that accelerate spoilage. These active packaging solutions help preserve the sausage’s flavor, color, and nutritional value, providing a better eating experience for consumers.
Eco-Friendly
Eco-friendly packaging solutions, such as compostable and recyclable materials, are gaining popularity as manufacturers seek to reduce their environmental footprint. For instance, some companies are now using packaging made from renewable resources like cornstarch or sugarcane, which can be composted after use, returning valuable nutrients to the soil. These materials not only reduce reliance on petroleum-based plastics but also help minimize waste and pollution.
Biodegradable packaging is another promising area. These materials break down naturally over time, reducing the burden on landfills and the environment. Innovations in bioplastics, such as polylactic acid (PLA) derived from plant sugars, are providing viable alternatives to traditional plastics. These materials offer similar protective properties while being environmentally friendly.
The push for sustainability is also driving innovation in packaging design. Manufacturers are exploring ways to reduce the amount of material used in packaging without compromising on protection. Lightweight packaging not only lowers material costs but also reduces transportation emissions, contributing to a smaller carbon footprint. Additionally, designs that enable easy separation of different packaging components facilitate recycling and improve overall sustainability.
Consumer Driven Innovation
Consumer preferences are also shaping the future of sausage packaging. There is a growing demand for convenient, easy-to-use packaging solutions. Resealable packages, portion-controlled packs, and packaging designed for on-the-go consumption are becoming increasingly popular. These features not only enhance consumer convenience but also help reduce food waste by allowing consumers to use only what they need and keep the rest fresh.
Conclusion
Sausage packaging is a complex process that involves various technologies and materials to ensure product quality and safety. From extending shelf life and reducing waste to enhancing packaging design and incorporating automation, there are many factors to consider. By staying informed about the latest innovations and best practices in sausage packaging, manufacturers can continue to meet consumer demands and contribute to a more sustainable future.
By following these insights, manufacturers can ensure their products not only reach consumers in the best possible condition but also stand out in a competitive market. The future of sausage packaging is bright, with continuous advancements promising even better solutions for both producers and consumers.
To learn more about how to build efficiency in your sausage packaging line, contact us today.