Introduction to Sausage Packaging: An Overview
Sausage packaging plays a crucial role in the food industry, ensuring product safety, accuracy, and efficiency. This article explores the various aspects of optimizing sausage packaging, including the use of centrifugal machines, the importance of food safety, counting and packaging techniques, cleanliness standards, total cost of ownership (TCO), overall equipment efficiency (OEE), and Velec’s innovative solutions.
The Importance of Food Safety in Processed Food
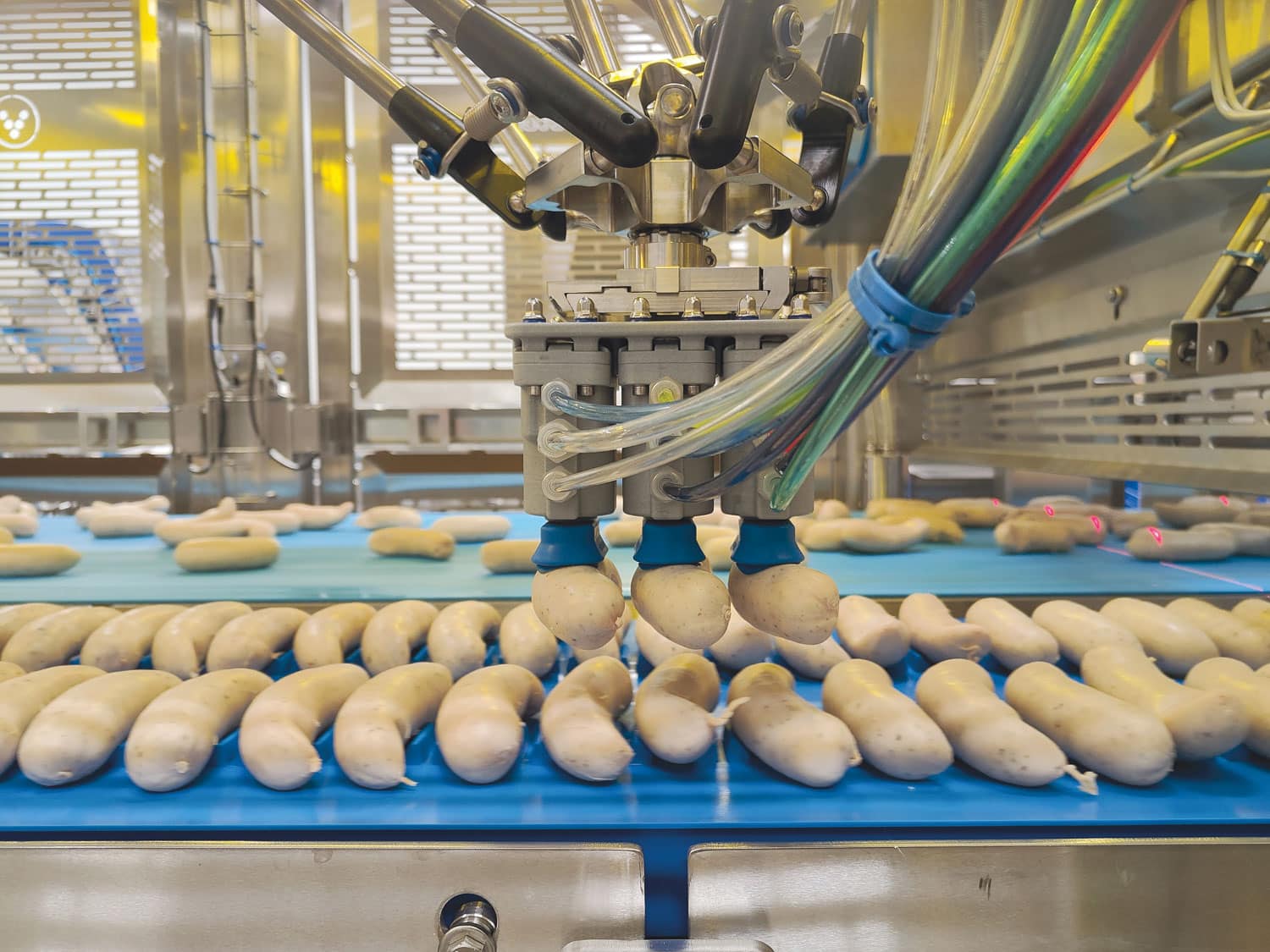
Food safety is incredibly important in the processed food industry, especially when it comes to sausage packaging. When sausages are contaminated or not packaged properly, it can pose serious health risks to consumers. That’s why it’s crucial to maintain high food safety standards throughout the entire packaging process to ensure that the sausages are safe to eat and of the highest quality.
Ensuring food safety starts with the ingredients used in sausage production. It’s important to source high-quality ingredients that are free from any contaminants or harmful substances. This includes selecting fresh meats and using spices and additives that meet strict safety regulations.
Proper handling and storage of ingredients is another critical aspect of food safety. It’s essential to store the product at the correct temperatures to prevent the growth of bacteria. Additionally, following hygiene practices, such as regular hand washing and wearing protective gear, can help minimize the risk of contamination during the packaging process.
When it comes to packaging sausages, using safe and hygienic materials is essential. Packaging materials should be designed to prevent any leakage or cross-contamination. They should also be resistant to moisture and bacteria to ensure the sausages remain fresh and safe for consumption.
Regular inspections and quality control checks should be conducted throughout the packaging process to identify any potential issues or deviations from safety standards. This includes monitoring the temperature and humidity levels in the packaging area, as well as conducting microbial tests to ensure the sausages are free from harmful bacteria.
By maintaining high food safety standards throughout the sausage packaging process, companies can not only protect the health and well-being of consumers but also safeguard their reputation and build trust in their products. It’s a responsibility that should be taken seriously to ensure that every sausage that reaches the market is safe, delicious, and of the highest quality.
Centrifugal Machines: Revolutionizing Sausage Packaging
Centrifugal machines have brought about a significant revolution in the sausage packaging industry. These machines offer advanced automation and precision, making the packaging process more efficient and reliable. In this section, we will explore how centrifugal machines handle the packaging process with great efficiency, ensuring precise counting of sausages.
One of the major advantages of using centrifugal machines is the increase in productivity. These machines can organize sausages at a much faster rate compared to manual methods. This not only saves time but also allows for higher production volumes, meeting the demands of the market more effectively.
Additionally, the use of centrifugal machines can lead to reduced labor costs. With automation taking over the packaging process, fewer workers are required to perform manual tasks. This not only saves money but also reduces the potential for human errors, ensuring consistent and accurate packaging results.
The precision offered by centrifugal machines is another significant benefit. These machines are designed to handle sausages with utmost care and accuracy, ensuring that each sausage is properly sorted and counted. This eliminates the risk of errors or discrepancies in the packaging, enhancing the overall quality and appearance of the final product.
Moreover, the use of centrifugal machines can contribute to improved packaging accuracy. These machines are capable of maintaining a consistent packaging standard, ensuring that each sausage is packaged in the same manner. This consistency not only enhances the visual appeal of the product but also helps in maintaining customer satisfaction and brand reputation.
In conclusion, the introduction of centrifugal machines has revolutionized the sausage packaging industry. These machines offer advanced automation, precision, and efficiency, resulting in increased productivity, reduced labor costs, and improved packaging accuracy. By embracing this technology, companies can streamline their packaging processes and deliver high-quality sausages to the market more effectively.
How do Velec’s Machines Improve Productivity and Safety?
Velec has developed a global sausage packing solution. The system starts with the completed sausages in bulk containers. These sausages must be properly aligned to package them for sale. The machine must also be gentle to avoid damaging the products. How can we accomplish this?
Velec’s solution places the bulk sausages into the centrifugal machine. This machine is designed to align the sausages without damaging them as quickly as possible. From the centrifugal machine, the sausages feed onto a V Conveyor and then onto what is called a piano belt. The piano belt carries them to the robotic cell. Along the way, each sausage can be inspected with an optical sensor, which uses modern machine learning to reject any malformed or damaged sausages before they get to packaging.
The robotic cell houses a high tech laser guided robotic arm to carefully place each sausage into the packaging. The arm is capable of quickly and accurately depositing one or more layers of sausages into the primary packaging. This system minimizes human contact with the product, greatly lowering the risk of contamination while increasing productivity.
Counting and Packaging: Ensuring Accuracy and Efficiency
In sausage packaging, it is crucial to have accurate counting and packaging to meet customer expectations and comply with regulatory requirements. This section focuses on the techniques and technologies employed to achieve precise counting and packaging, minimizing errors and maximizing efficiency. We emphasize the significance of advanced counting systems and automated packaging equipment in streamlining the process, ensuring that sausages are packaged accurately and efficiently. By utilizing these innovative tools, companies can enhance their productivity and deliver products that meet the highest standards of quality and precision.
Cleanliness Standards in Food Processing Equipment
Ensuring cleanliness and hygiene in food processing equipment is essential to prevent contamination and guarantee the safety of products. This section highlights the importance of adhering to rigorous cleanliness standards in sausage packaging. We emphasize the significance of regular equipment cleaning, following sanitation protocols, and utilizing hygienic materials to maintain a clean processing environment.
Regular equipment cleaning is crucial to remove any residual food particles or bacteria that may accumulate during the packaging process. By implementing a thorough cleaning schedule, companies can minimize the risk of cross-contamination and maintain a hygienic production environment.
Sanitation protocols play a vital role in maintaining cleanliness. These protocols include procedures for cleaning and sanitizing surfaces, equipment, and utensils. By strictly following these protocols, companies can ensure that all components involved in the packaging process are free from contaminants.
Velec’s machines use clean in place (CIP) technology to enhance food safety. The benefit of CIP is that it nearly eliminates the risk of manual error during the cleaning process. The operator simply launches the cleaning program and the machine automatically applies the required sanitation protocols for the appropriate time. CIP is also more efficient, and uses up to 50% less water than manual cleaning.
Using hygienic materials is another key aspect of maintaining cleanliness. Packaging materials should be designed to prevent the growth of bacteria and should be resistant to moisture and other potential sources of contamination. By selecting appropriate materials, companies can minimize the risk of product contamination and uphold high hygiene standards.
By prioritizing cleanliness and hygiene in sausage packaging, companies can safeguard the quality and safety of their products. Adhering to strict cleanliness standards, implementing regular equipment cleaning, following sanitation protocols, and utilizing hygienic materials are all crucial steps in maintaining a clean processing environment and ensuring consumer confidence in the final product.
Understanding Total Cost of Ownership (TCO) in Food Processing
Understanding the concept of Total Cost of Ownership (TCO) is crucial when making investments in food processing equipment, including sausage packaging. This section aims to explain the importance of TCO and its relevance in the context of sausage packaging. We will delve into how evaluating the long-term costs associated with equipment, such as maintenance, energy consumption, and downtime, can empower businesses to make informed decisions and optimize their overall operational efficiency.
TCO encompasses more than just the initial purchase price of equipment. It takes into account the total costs incurred throughout the equipment’s lifecycle, including installation, maintenance, repairs, energy consumption, and even potential downtime. By considering these factors, businesses can gain a comprehensive understanding of the true cost implications associated with their equipment investments.
Analyzing the TCO of sausage packaging equipment allows businesses to make informed decisions based on the long-term costs and benefits. For example, investing in equipment that requires less maintenance and consumes less energy can result in significant cost savings over time. Additionally, choosing equipment with a lower risk of downtime can help minimize production disruptions and maximize operational efficiency.
By evaluating the TCO of food processing equipment, businesses can optimize their investment decisions and ensure long-term profitability. It allows them to identify cost-saving opportunities, improve operational efficiency, and ultimately deliver high-quality sausage products to the market in a cost-effective manner.
The Role of Overall Equipment Efficiency (OEE) in Sausage Packaging
Overall equipment efficiency (OEE) is a metric used to measure the performance of manufacturing equipment. In this section, we explore how OEE can be applied to sausage packaging processes. We discuss the key factors affecting OEE, such as equipment availability, performance, and quality, and how optimizing these factors can enhance productivity and reduce costs.
The Future of Sausage Packaging: Velec’s Innovative Solutions
By staying at the forefront of industry trends and continuously improving their solutions, Velec aims to shape the future of sausage packaging.
Optimizing sausage packaging involves various factors, including the use of centrifugal machines and robot loader, ensuring food safety, accurate counting and packaging, maintaining cleanliness standards, understanding TCO, considering OEE, and embracing innovative solutions. By prioritizing these aspects, the food industry can enhance product quality, safety, and operational efficiency in sausage packaging processes.
Ready to improve efficiency, cleanliness, and lower your TCO? Contact us today to learn more about how to improve your sausage production line.