Understanding ‘Global Packaging’ in Food Processing
A global solution in food packaging means one that includes every step in the process. Things like elevators, conveyors, vertical loaders, and automated baggers are both hygienic and more efficient. Read on to learn about how a global solution can improve your factory line.
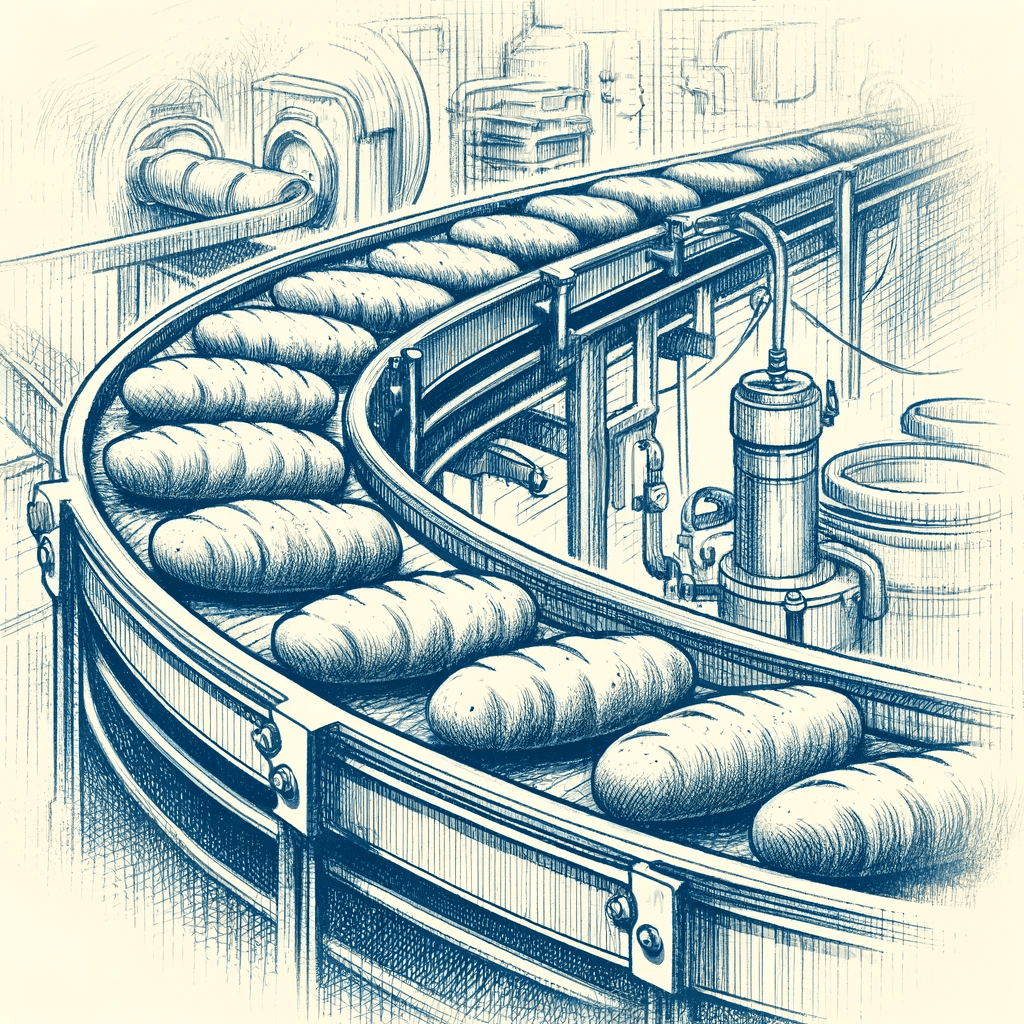
The Role of Elevators and Conveyors in a Complete Line
In food processing, elevators and conveyors move raw materials, ingredients, and finished products throughout the production cycle. Elevators move the product from a lower space to a higher one. This is important because many packaging machines load at the top and dispense from the bottom. This means the product must be raised to the top of the machine for the line to continue.
On the other hand, conveyors move things horizontally. Both swiftly transfer products between different processing stages with precision and speed. Conveyors automatically keep the product and ingredients constantly moving from one step to the next.
Integrating elevators and conveyors into a complete processing line offer you several benefits. First, it boosts overall productivity by accelerating material and product movement, reducing downtime and increasing output levels significantly. Second, the adoption of elevators and conveyors minimizes manual handling, leading to improved workplace safety standards and operational efficiency.
These systems play a vital role in upholding product quality and consistency throughout the production journey. Elevators and conveyors help materials and products move smoothly and in an organized way. This stops things from getting contaminated, damaged, or mixed up, making sure the final products are just as good as they’re supposed to be.
Elevators and conveyors drive efficiency, productivity, and quality within food processing operations. They streamline processes and reduce operational costs while enhancing your competitive edge.
Vertical Loaders: A Game-Changer in Food Packaging
The introduction of vertical loaders has brought about a major change in how food is packaged. These new machines load items into packaging containers vertically, revolutionizing the industry. They’re designed very carefully to do this with incredible accuracy and efficiency.
Vertical loaders make things simpler. This reduces the need for manual work, lowers the chance of products getting damaged, and makes the whole process faster.
Vertical loaders are especially helpful for handling delicate or oddly shaped products like baked goods, snacks, or medicines. Many of these need to be placed just right in their packaging. Their ability to handle these products carefully and accurately adds a touch of sophistication to the packaging process, making sure the products stay intact and look good.
Using vertical loaders in your packaging lines brings several benefits. These machines not only make packaging faster and more accurate but also make the whole operation more efficient. By improving how things are loaded and making sure products are placed perfectly, vertical loaders help improve how products look and make customers happier.
Flow Wrap and Thermoforming: Revolutionizing Food Packaging
Two other relatively recent innovations in food packaging are flow wrap and thermoforming. Flow wrap is also called a horizontal loader. The packaging is similar to what is produced by a vertical loader. Flow wrap packages products in plastic or aluminum foil, sealing them to maintain freshness and prolong shelf life.
Thermoforming utilizes heated plastic sheets to craft containers and trays, offering both protection and visibility for food items. Both flow wrap and thermoforming are efficient and flexible solutions that cater to a diverse range of food products.
The introduction of flow wrap and thermoforming methods has drastically changed how food is packaged. These methods provide packaging that can be customized, strong, and looks good, meeting the unique needs of different types of food. This flexibility lets food companies change the packaging to fit different products, making them more attractive to customers and reaching more people.
Using these new technologies, you can make your packaging faster, more efficient, and keep the quality of the products high. This helps them keep up with what customers want in today’s competitive market. Using flow wrap and thermoforming shows a dedication to being innovative and doing a great job in food packaging.
Integrating Global Solutions for a High-Performing Factory Line
When you bring global solutions into your food factory line, you’re combining standardized processes, the latest technology, and top-notch equipment to create a smooth and efficient production system. By using global solutions like standard packaging machines, automatic palletizers, and advanced food processing equipment, you can maintain the same quality standards across different lines and even different production sites.
This smart integration helps you manage your resources better, cut down on time when things aren’t running, and make more products while still keeping a close eye on important things like product safety and quality. By putting global solutions into your factory lines, you can make your operations run better, keep your products consistent, and stay competitive in the global market.
With these solutions in place, you can strengthen your position in the market, come up with new ideas, and meet the changing needs of customers everywhere, setting yourself up for growth and success in the food industry.
Clean in Place Equipment: Enhancing Food Safety and Operational Efficiency
In food processing, Clean in Place (CIP) equipment is important for keeping things clean and safe. CIP systems are made to clean and sanitize important equipment, pipes, and tanks without needing to take them apart. This makes cleaning easier, faster, and more thorough. Many times CIP is completely automatic, meaning it happens after every run of food or at the end of every day.
Using CIP equipment helps prevent problems like contamination and bacteria, which keeps your products safe and your customers healthy. By using CIP technology, you make your workplace cleaner and safer and make sure you’re in compliance with industry standards and health laws.
CIP systems clean automatically, which saves water and chemicals and is better for the environment. Also, having CIP equipment helps food processing facilities clean better, reduce downtime, and make everything run smoother while still meeting the high standards of the industry.
Overall, Clean in Place equipment is an important tool in modern food processing. It combines technology and cleanliness to keep food hygienic and operations top-notch, setting a high standard for cleanliness, efficiency, and following the rules in the ever-changing world of food processing.
Future Trends in Global Solutions for Food Processing
The future of global solutions in food processing is changing. There’s a mix of new technology, a focus on being eco-friendly, and more machines doing the work. These things are shaking up how things are done in the industry.
Some of the top changes come from cool technology like artificial intelligence, the Internet of Things (IoT), and robots. These are making food processing better by making things more efficient, keeping track of where things come from, and making sure the quality is top-notch.
At the same time, there’s a push to be more eco-friendly. This means using things like packaging that can break down, finding ways to make less waste, and using machines that use less energy. These efforts show that food processors care about the environment and want to use resources wisely, matching what people want these days.
Also, more machines are doing the work in food processing. Things like robots that stack pallets, smart sensors, and tools that predict when machines need fixing are becoming more common. This means operations are getting better, costs are going down, and new ideas are popping up in processing plants.
By using these new trends and being open to new ideas, food processors can stay ahead in the industry. They can adapt to what customers want, be leaders in innovation, and deal with all the changes in the food processing world.
Does your factory line use a global solution? Speak with one of our experts today to see how you can gain efficiency and increase your bottom line.